Understanding the Laser Pneumatic Version
The Laser Pneumatic Version of our Auspicious feather balloon toy is an innovative piece of equipment designed for enhanced creativity and fun. Engineered with cutting-edge technology, it offers remarkable buoyancy, engaging aesthetics, and intricate details that attract both children and adults.
This versatile machine comes equipped with key features like automated calibration, precision controls, and high-powered lasers coupled with pneumatic mechanisms. Typical applications span across various industries including toy manufacturing, education, and entertainment events where creative displays are crucial.
Importance of Safety in Laser Operations
Operating any laser equipment entails potential hazards that must be conscientiously managed. Lasers can cause severe injuries such as burns or eye damage if handled improperly. Understanding these risks is essential for maintaining a safe workspace.
There have been numerous case studies pointing out the grave consequences of inadequate safety measures; for instance, mishandling laser-equipped devices has led to accidents causing visual impairment and other serious health issues. Therefore, prioritizing safety protocols cannot be overstressed.
Pre-Operational Safety Measures
Personal Protective Equipment (PPE)
Before operating the Laser Pneumatic Version, it's vital to equip yourself with appropriate Personal Protective Equipment (PPE). Essential items include:
- Safety goggles to protect eyes from harmful laser exposure.
- Heat-resistant gloves to prevent burns during handling.
- Face shields for comprehensive facial protection.
Ensure regular checks and maintenance on your PPE to guarantee its effectiveness throughout the operational period.
Workspace Preparation
A clean and organized workspace minimizes risks and allows for smoother operations. Beyond tidiness, ensuring adequate ventilation aids in dispersing fumes. Suitable lighting is also paramount for visibility and precision.
Always verify that emergency exits are accessible and well-marked. Moreover, having first aid kits strategically placed can expedite response times should an incident occur.
Machine Setup and Inspection
Initial Inspection Checklist
Prior to powering up the Laser Pneumatic Version, conduct an extensive inspection checklist:
- Check for any physical damages or signs of wear.
- Examine electrical and pneumatic connections to ascertain their integrity and functionality.
Calibration and Configuration
Proper calibration is critical for optimal performance. Follow the manufacturer’s guidelines meticulously when calibrating the device. The settings need customization according to the specific materials and tasks at hand for precision and safety.
Follow this step-by-step guide to effectively power up the machine:
- Verify all inspections are complete.
- Connect to a secure power source.
- Initiate system startup using the main control panel.
Perform a final sweep of safety checks before commencing operations to identify any tentative vulnerabilities.
Maintain a prudent distance from the laser emitter to avoid accidental exposure. Never look directly into the laser beam, regardless of whether you perceive it as active or not.
Continuously monitor the machine's performance, staying alert for unusual sounds or irregular functioning which could indicate underlying issues.
Recognize warning signals promptly—unusual odors, strange noises, or visible malfunctions require immediate attention. Initiate rapid response by shutting down the equipment safely and consulting trained personnel.
When powering down the Laser Pneumatic Version, adhere to structured steps:
- Switch off the laser and disconnect power sources securely.
- Ensure the area is clear and inform necessary team members about any incidents.
After use, follow systematic shutdown procedures. Thoroughly clean and maintain the machine to prevent residue buildup and wear.
Accurate records of operational data and any incidents play a crucial role in ongoing safety management. Report any maintenance needs immediately to facilitate prompt resolution.
Regular training ensures that operators are abreast of the latest safety practices. Organize frequent sessions and drills to solidify knowledge and preparedness.
Encouraging feedback from operators helps pinpoint areas needing improvement. Implement actionable changes based on authentic insights and detailed incident reports.
Refer to the manufacturer's safety guidelines and industry-best standards to uphold operational excellence. Detailed manuals offer invaluable information for both novices and experienced handlers.
If additional support is required, contact the manufacturer’s customer service for specialized assistance. For urgent matters, local emergency services and safety authorities gather comprehensive intervention expertise.
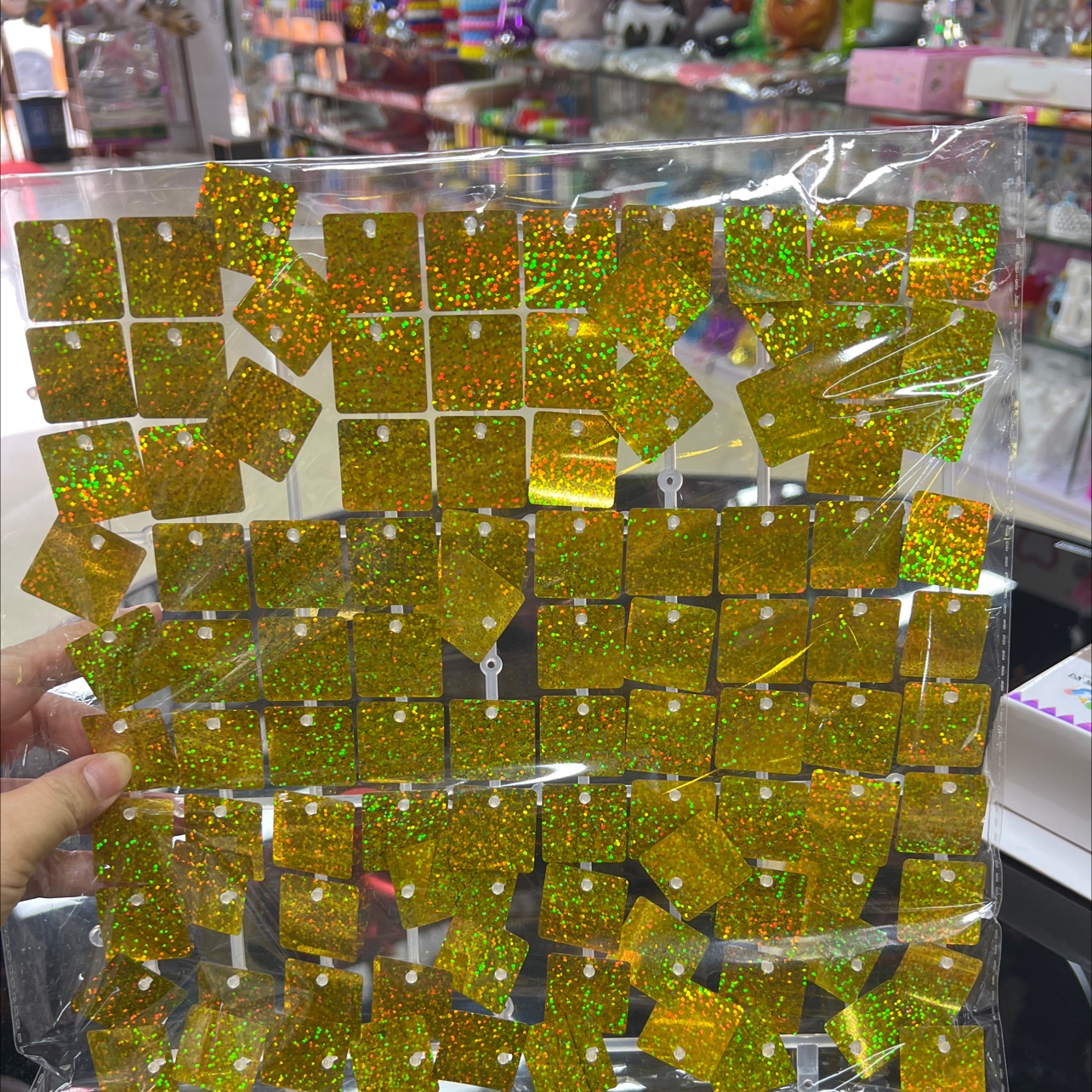